PSC Flooring have been providing manufacturers with industrial flooring solutions for many years. As all businesses know there comes a point whereby you must invest in the future to secure the business in the long term. In 2021 PSC have made significant investment in the company’s long term future. We did this by expanding the workforce, company vehicles, machinery and equipment.
Investing In Machinery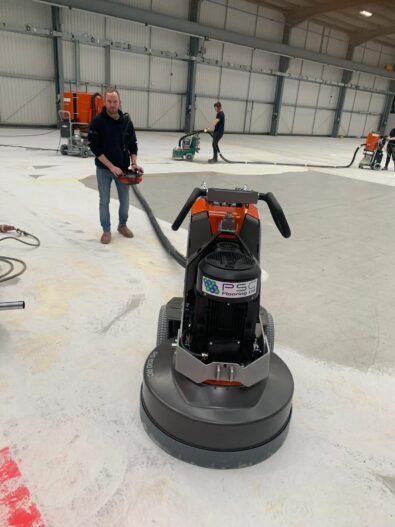
With the help of the Worcester County council PSC Flooring secured grant funding. Therefore, enabling us to invest in the latest technology in diamond grinding equipment. Traditionally due to the limitations of existing machinery, preparation work of highly dense concrete, has been undertaken by close working partnership subcontractors. This type of work was always done by the use of a shot blasting machine. This is because traditional diamond grinding machines were not suitable/robust enough for this type of preparation. Therefore, this type of work had to be outsourced.
The Right Tools For The Job
The secured grant funding enabled us to purchase the new Husquivana PG830 remote 3 phase floor grinder and Husquivana D80 3 phase dust extractor. Consequently, this enables us to take on larger floor preparation work. Specifically, the preparation of newly laid and highly dense power floated concrete floors. In addition, the purchase of this latest technology in diamond grinding equipment, means that PSC can prepare highly dense concrete in house.
First Outing… Expert Tooling
Expert Tooling of Coventry have been long term clients of PSC Flooring. They are leading manufacturers of industrial automation systems, assembly tooling, automated assembly and special purpose machinery. As well as, single and multi-robotic cells, including robotic assembly. We have previously installed a high build, epoxy resin flooring system to their 1350sqm production area floor approximately 4 years ago. As Expert Tooling were moving machinery, it made sense to refresh the floor whilst the floor space was clear. Therefore, they asked PSC to come in and refurbish the area.
Engineering & Manufacturing Flooring
The manufacturing floor itself was in good condition. However, even so, the preparation process included a thorough cleaning and preparation of the existing resin floor surface. Subsequently, this was done using the new Husquivana PG830 remote 3 phase floor grinder, Husquivana D80 3 phase dust extractor and the handheld 110v diamond grinder. As per the normal process all dust and residues were then vacuumed clear. Additionally, repairs were made to any localised damaged concrete, holes, bolt holes as required using a resin filler.
Manufacturing Floor Fully Refurbished
The two coat Resdev Pumatect high build, epoxy resin flooring system was applied to the 1350 square meter area. The clients chosen gloss was light grey, Ral 7035. After the flooring cured, we applied the 75mm wide Epoxy resin demarcation lines. This was done in safety yellow Resdev Pumatect V high build epoxy resin. Furthermore, the whole job took just 4 days to complete.
Trevor Canning of Expert Tooling commented:
“Once again PSC have made an excellent job of the production floor. This is a high traffic area, and it is important that we maintain high standards of cleanliness to prevent health and safety incidents.”
If you enjoyed reading this blog or found it useful why not take a look at a previous blog: Surface Preparation | The Key Successful Floor Installation. Additionally, get in touch today to discuss you need for industrial flooring solutions. Whether you need flooring for a warehouse or manufacturing flooring, we can help.